Totally Turning Demonstrators, March 29 & 30, 2025
International/National:
Kirk DeHeer | Jim Echter | Kristin Levier | Art Liestman | Keith Tompkins
Regional:
Rick Angus | Stan Blanchard | Rich D’Ambrosio | Todd Gunter | Ray Puffer
Please check back for updates as we add presenters.
_________________________________________
Click here to see a list of demonstrators from previous years.
International/National Demonstrators
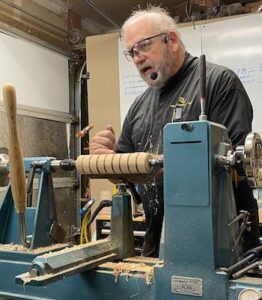
Kirk DeHeer
Demonstrations
Tool techniques for turning a Calabash bowl
This demo shows the tools and techniques used to turn a green wood round bottom bowl. This demo has a lot of tool techniques and tips and tricks that will help every turner regardless of skill level. In this demo I like to show the tool techniques used to cut the wood in a way that is pleasing to the wood. This also shows the efficiency of the lathe. Topics covered: Woodturning safety. Calabash bowl design. Tools used and the grinds. Mounting the wood to the lathe. Cuts used to rough out the shape. Cuts used to refine the shape. Cuts used on the inside of an undercut shape. Removing the evidence of how the bowl was held on the lathe
Demystifying Hand thread chasing
We discuss the tools and materials needed for hand thread chasing, With an easy to follow explanation of how to Hand chase threads. Along with turning a heirloom threaded box. Techniques covered. Safety Mounting the blank. Thread chasing speed. Thread chasing tools. Wood suitable for thread chasing. Both inexpensive practice wood and heirloom boxes. Hollowing endgrain. Thread chasing. Matching the grain.
Turning a Bowl and a Platter
Turning a Bowl and Platter present different challenges. We discuss the differences and how to approach them in this demo. Techniques covered: Turning safety. Bowl and Platter design. Turning efficacy AKA sequencing. Mounting the blank. Getting a safe hold on your blank. Tool selection. Where and when to switch from a bowl gouge to a scraper.
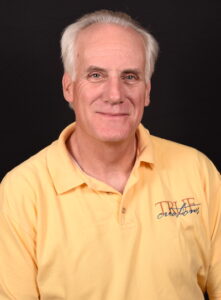
Jim Echter
New York, USA
True Creations Woodturning
Jim is a production turner, instructor and writer that has developed a series of wooden tools for fiber artists that he wholesales around the world. He specializes in architectural restoration work and turning custom and replacement furniture components. Woodturning started as a hobby for Jim over 49 years ago and evolved into a career twenty years ago. He markets his products and services through retail outlets and his True Creations Woodturning web site: www.tcturning.com. He also conducts private instruction at his studio and has taught and demonstrated for over 90 woodturning groups. In 2019, Jim demonstrated at the AAW Symposium in Raleigh and was a featured live demonstrator for the 2020 Woodturners Worldwide Online Symposium where his Sensational Skew program received outstanding reviews by the attendees. He also demonstrated at the 2022 AAW Symposium in Louisville.
With his manufacturing engineering degree, understanding of tool steels and grinding angles, and his skill for explaining tool/body movement when woodturning, Jim has developed a passion for teaching woodturning skills for all levels of student abilities. He is especially known for reintroducing the joys and benefit of learning spindle turning and in particular, the skew. Once spindle turning is mastered, Jim is confident you will become a more efficient and better bowl turner.
Jim was the founding President of the Finger Lakes Woodturners Association chapter of the AAW which is now over 170 members strong. Prior to the start of FLWT, for two different three year terms, he chaired the Woodturning Special Interest Group for the Rochester Woodworkers Society which, at that time, was the largest woodworking guild in the country. He has been an active member, board member, demonstrator and contributor to the woodturning scene for over 46 years.
Demonstrations
“Spindling” Your Way to Better Bowls
If you’ve made a few basic bowls or simple platters and now want to progress so you can refine your profiles and add details like beads and coves, then “Spindling” is the easiest way to develop the skills needed. For hundreds of years, woodturning apprenticeships taught spindle turning before face grain turning. The reason is the turner developed much better tool control and a feel for how wood likes to be cut. These skills can easily be transferred to bowl turning, taking your projects to the next level. This program will walk you through the basics on how to teach yourself spindle turning and how to apply those skills to enhance your bowls. The tools and their proper use will all be demonstrated and a series of practice exercises will be shown.
Beginner, Intermediate and Advanced
Mini Lathe Friendly
The Sensational Skew
Back by popular demand, in this demonstration Jim will take the mystery out of how to use the skew so it becomes the sensational tool in your arsenal. Utilizing a combination of images, large scale models and actual demonstrations, the use of the skew will be broken down into very understandable bites of information. The program will overview skew profiles, edge profiles, sharpening procedures, basic cuts, advanced cuts, and learning exercises. Project ideas will be demonstrated that will help you build confidence with using this sensational tool.
Beginner, Intermediate and Advanced
Mini Lathe Friendly
40 Tips for Mounting Blanks on Your Lathe
Jim will examine over 40 tips for mounting blanks on your lathe that he has accumulated over the almost 50 years’ experience. He will explore modifying tips, making special tips and how to turn thin spindles. Next he will review faceplate modification and friction driving blanks. Then, Jim will review the mechanics behind using 4-Jaw chucks for maximum holding power and safety. Finally, Jim will demonstrate and show several special techniques he has developed for holding all sorts of projects.
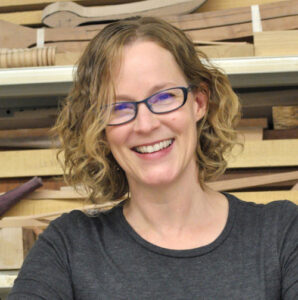
Kristin Levier
USA
Artist Kristin LeVier is a former molecular biologist who creates work at the intersection of art, nature and science to remind us of our connection to the breathtaking spectacle of the natural world. Her organic carved and bent wood sculpture embodies an ethereal sense of motion. She spoke about her work in a TEDx talk on The Art of Science and in a PBS short feature. Her award-winning work has been exhibited widely and featured in books and magazines such as American Craft and American Woodturner. She teaches craft and design at symposia and at craft schools including Anderson Ranch, Arrowmont and the Center for Furniture Craftsmanship. Her studio is nestled among stunning rolling hills in Moscow, Idaho.
Demonstrations
Adding Sculptural Elements to Your Turnings
Learn methods for seamlessly adding sculptural elements to your turnings using simple joinery and carving techniques. Kristin will demonstrate how she creates curved appendages that emerge from turned objects and securely joins carved and turned objects together. Learn simple design and modeling tricks to allow you to create your most successful sculptural work.
Bending Wood Without Steam: Introduction to Compressed Hardwood
Compressed hardwood is regular hardwood that has undergone a treatment involving steam and compression, allowing it to be bent by hand while at room temperature. This amazing wood can be turned or added to woodturned objects to stunning effect. Kristin has been using compressed wood for more than fifteen years and shares a trove of techniques and lessons learned.
Introduction to Micromotor Power carving
If you’ve been curious about power carving but didn’t know where to start or what to buy, this demonstration is for you. Topics covered include types of carving, micromotor units (available brands, how to use), carving burrs, safety, wood choices, and technique.
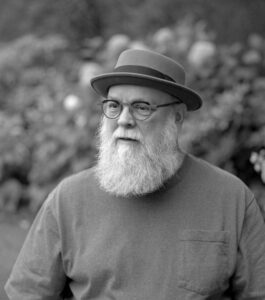
Art Liestman
British Columbia, Canada
I’m a wood artist living in Coquitlam, British Columbia. My work has been seen in numerous exhibitions and galleries across North America and has appeared in numerous books and magazines.
I began working with wood when I was a graduate student. At that time, I was interested in designing and making experimental musical instruments. After moving to BC, I joined the local woodworking club. One of the most interesting things that the club did was to hold an annual 2×4 challenge in which members were challenged to make something using only an 8 foot long 2×4, glue, and finishing products. One of the 2×4 projects that I decided to make was an automated programmable xylophone. It needed some roundish parts which was a good enough excuse to add a lathe to my tool arsenal.
While completing that instrument, I quickly discovered that turning wood on the lathe was addictive. At that point, I began to focus on woodturning rather than instrument building. I spent a few years making the usual functional turned items, but a demonstration by Frank Sudol opened my eyes to the possibilities of expression in artistic woodturning. After taking a particularly illuminating class with Jacques Vesery, I starting making my puzzling illusion vessels. Since then, my life in wood art continues to evolve.
In addition to the puzzling illusion, I’ve enjoyed exploring other surface enhancements using burning, pyrography, carving, and coloring. I have a particular interest in making pieces on the lathe that do not necessarily appear to be turned. I’m not opposed to working off of the lathe, but virtually every piece that I make is based on a turned form.
Demonstrations
The Lost Wood Process
I turn spindle blanks that are made up of three laminated layers. After turning, the middle layer is removed and the two outer layers are rejoined to give a turned object that isn’t round. As an example of this process, I show how to make a standard turned box that ends up being almond shaped in cross-section (inside and out). The demo shows the glue up process (including grain matching), turning the box, disassembling and reassembling the layers.
Therming
I discuss the construction of jigs and show how to use them to turn multiple curved surfaces on wood blanks. This is a variation on multi axis turning in which the axis of rotation does not lie within the blank being turned. More details can be found in my American Woodturner article. As an example, I show how to make a turned teapot body which is turned on 5 different axes, producing a four sided hollow teapot body.
Flame Texturing of Highly Figured Wood
I show my technique for “flame texturing” highly figured wood. The textured wood can either be left “as is” or coloured with multiple layers of acrylic paints using a dry brush technique or a combination of airbrushing and dry brushing. As an example, I turn, flame texture, and colour a “popcorn bowl” which ends up looking like stone. Burning and dry brushing are shown in detail, and a doughnut chuck is described and used.
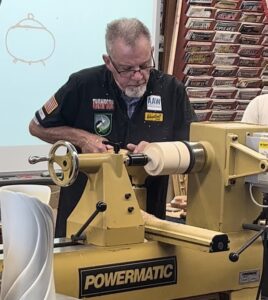
Keith Thompkins
USA
Keith began his woodworking career immediately upon graduating from high school, obtaining employment in a cabinet shop. His interests have gradually gravitated to working on the wood lathe, which allows him to explore his creativity to the fullest. Keith’s award-winning work was featured in Del Mano Gallery in Los Angeles, CA for over ten years, and his turnings have sold to collectors world-wide. Keith has demonstrated throughout the United States, Canada, and as far away as New Zealand.
Demonstrations
Multi-axis bottle stopper
In this demo I will turn a martini glass shaped stopper which appears to sit on two corks. I will demonstrate end-grain turning for the martini glass, and show how to get glass-smooth end grain cuts when turning the “corks”. The “corks” will be colored and textured to resemble real corks. The main emphasis of the demo is to show that multi-axis turning can be a useful and repeatable part of your turning skill-set and that there is no limit to your imagination when designing a turning…even a lowly bottle stopper.
Essential cuts on the lathe
Beginner turners often find that woodturning is a daunting task; often holding their tools in a death-grip while hoping to avoid a catch. In this demo I will show the basic cut I employ to create my work. I will focus on the spindle gouge, bowl gouge, and skew chisel, showing how to get clean work, free of torn grain. Turning beads, coves, and filets will be covered, as well as end-grain techniques. Anyone who is new to turning, or turners who are experiencing difficulties in tool control or having issues with ton grain will benefit greatly from this demonstration.
Things that cannot be turned on a lathe
This will be a fun demonstration! I discovered years ago that a cube can be turned on the lathe; yes, with it running! Since then, I have expanded upon the idea; in this demo we will turn not only a cube, but a curved tube which is hollowed all the way through. To make it a little more interesting, we will turn a curved square-profile tube, with a square hole all the way through. I will then demonstrate how to create one of my signature spiral forms on the lathe. This will be a fun demo, but it will expand your ideas of what actually CAN be turned on the lathe.
Regional Demonstrators
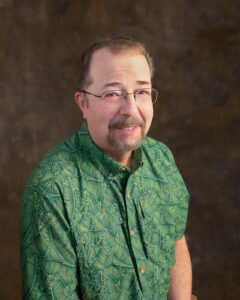
Rick Angus
USA
Rick Angus enjoys turning wood and understanding the details of efficient tool handling. (A sharp tool can be a wonderful dance partner if properly led.) Acquiring skillful technique with sharp tools improved his joy of woodturning immensely and allowed him to focus on design and shape of the objects being created.
During his formative years of turning, Rick learned the regimented classical spindle techniques from Alan Batty and George Hatfeld with cross-grain bowl and hollow-form techniques learned from David Ellsworth and John Jordan—amongst many others.
Formally trained as an organic chemist, Rick uses his scientific curiosity to investigate the art of woodturning in the analytical way of a scientist. The result is an analysis of how tools work and the ability to put them to work in the proper manner. In addition, he studied design and visualization techniques from the art community.
His work began mostly with cross-grain open bowl forms produced from half log segments. The grain patterns are chosen for symmetry—or not! The addition of long-grain (spindle) vessels such as vases and lidded boxes allowed the expression of a much taller hollow form. Incorporating lids to these vessels has been quite a bit of fun. Most recent work has focused on spindle turning with finely sharpened tools. Smooth graceful shapes with sharp detail are his hallmark.
Demonstrations
End-grain Lidded Box with Contrasting Wood Inset at Joint
End-grain boxes made from one piece of wood are fun to make and a delight to open to see what is inside. Woods with attractive figure, color or grain lines interest me the most. One challenge to designing these boxes is the matching of figure or grain lines at the joint between top and bottom of the box. Since the solid piece of wood must be parted into two pieces to remove the wood from the interior, the wood lost to the parting process also removes some of the figure, color or grain lines that originally attracted me to the stock. This parting cut becomes the joint between the top and bottom of the finished box. Upon reassembly of the box, one often finds that the interesting pattern is disrupted at the joint; many people find these mismatching lines distracting and unappealing. By insetting a piece of wood, the same dimension as the wood in the joint, the mind ‘sees’ the original pattern even though it is interrupted by a contrasting segment. By increasing the contrast between the main wood of the box and the inset piece, the disruption of the interesting features that led me to choose this wood become minimized. This feat is accomplished by creating the boxes external shape from a single piece of wood, locating the position of the joint, parting the piece at the joint line, shaping the interior of the two pieces and to one piece, adding the inset. The inset is made from an end-grain piece of contrasting wood disk of suitable size, fitted it into the joint of one section of the box (top or bottom, depending on design) using loose mortise and tenon joinery. (The joint is not glued as in furniture construction but is left snug or loose depending on the desires of the maker.) The exposed part of this inset piece can be the same dimension as the parting cut used to separate the top from the bottom of the box or larger as you wish. The simple act of adding the contrasting inset gives us the option to add another feature to the box design. While the insert may fill the lengthwise void left by the parting cut, it need not be of the same profile as the rest of the box. For example, a protruding bead of contrasting wood may be included to provide a gripping point to the lid (or bottom!) or a recessed ring may be used to add a shadow line to the
Total Tool Control
Join me for an adventure investigating/exploring the fine details of how tour tools cut the wood. Our focus is on the interaction of the bevel and the knife edge as it with the wood and how to use this knowledge to slice chips from the bulk of the wood, leaving behind a baby-skin smooth surface. Since cutting wood requires forcing a hard, sharp tool into the fibers of wood, something must give. The wood yields to the harder steel as it penetrates the wood, and wood gets damaged by compression. We learn how to aim and guide the tool in the way that forces all the yielding of the wood to occur on the chip side of the bevel. This leaves the desired smooth surface on our pieces while putting all the damage to the wood into the chip.
We investigate the entire cutting surface of all the major woodturning tools. This includes spindle roughing gouges, chisels and other gouges; hybrid tools such as the skew gouge and the point tool; a variety of scrapers such as flat-0º-rake and negative-rake scrapers. We even learn the power of a (not-so-traditional) card scraper for leaving a terrific finish on cross-grain turnings. The value of controlling the many profile shapes and bevel angles of our tools is immeasurable. There is a wide range of bevel angles possible for each type of tool; we look at the range critically to find that each tool type has a small range of angles that fall in the general category—these all will provide good service for the usual tasks—and how the extreme angles of the range can be useful in specialty situations. Through a thorough understanding of how to view the actual cut and not just the chip, you can benefit from the best control of your tools possible. With this knowledge, you can choose from the broad range of tool profiles and bevel angles available to put the most beneficial tools for your tasks in your bag-o’-trix. This is the most important demonstration that you didn’t think that you needed.
Turning Utilitarian Goblets with a Cross-Grain Base
Goblets made from wood are a treat to use and make great gifts for a special occasion. Making then is fun and the process adds end-grain hollowing to standard spindle turner’s repertoire. The cross-grain base introduces added durability to the goblet. The project begins with orienting the center of the billet on one grain line; this we do by marking the center at one end and following that grain line on that center point out to the edge, along the edge and back across the other end of the billet before making the second center point. This assure that the thin stem of the goblet will follow a single grain line from stem to bowl. With the billet thusly mounted, we reduce the wood to a cylinder and mark the position of the goblet bowl, stem and foot. From here, the exterior of the bowl of the goblet is roughly shaped and the interior is hollowed and finished. (For a “Toasted” interior finish, the interior of the bowl is lightly burned with a torch; this adds a smoky flavor that enhances some beverages. Examples of “toasted” bowls will be shown though the actual burning will not be demonstrated.) Wall thickness is then reduced, and final shaping done to complete the bowl portion of the goblet. With tail support of the bowl, the stem is shaped. A cross-grain base is made using a custom wooden chuck and has a hole through the center. The stem is glued into the base to complete the goblet. A little fine sanding completes the project.
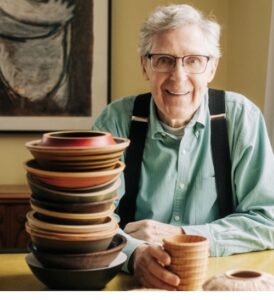
Stan Blanchard
USA
Stan earned his MFA in Photography in 1968 from Ohio University and spent 18 years as an industrial photographer with GE. After that career he started his own photography business and retired after 22 years. He has been a woodturner since 2010 and studied with David Elsworth and Al Stirt besides taking numerous classes sponsored by Northeastern Woodworkers Association. Much of the wood he acquired was excellent for turning but lacked interesting grain or patterns so he began using milk paint to embellish and decorate the bowls.
Demonstration
Milk Paint
Stan will demonstrate using milk paint on a turned surface. He will discuss the special tools he has found that work best for mixing the paint to a consistency needed for a smooth application to the workpiece. Special storage containers facilitate maintaining paint ready to use, eliminating the need to mix up new dry colors each time one has a surface to embellish. Methods of applying and refining the milk paint on the wood will be demonstrated with design possibilities discussed.
Rich D’Ambrosio
USA
Rich began woodworking at the age of 12 in his father’s workshop, soon becoming proficient with the scroll saw. Within a few years he advanced from fretwork to intarsia, before turning his first pen in his mid twenties. From there he moved on to bottle stoppers and, after several lathe upgrades, bowls. His trip down the rabbit hole began when he started using resin to fix cracks and add color to projects. When he first saw hybrid pen blanks, he loved everything about them except the price. Learning to cast his own blanks has led to all sorts of innovation.
Demonstrations:
Countertop epoxy techniques adapted for woodturning
You may have seen people making exotic stone patterns with epoxy. In this class you will learn how to take these techniques and apply the patterned epoxy to bowls and platters. The result is stunning and colorful embellishments to your turnings.
Hybrid pen from start to finish
We will discuss how to select wood and resin to make a hybrid blank, as well as which resins work best for casting, and what equipment is needed. This process easily scales up to make larger blanks, such as bottle stoppers, vases, and bowls. Finally, we will learn how to turn and finish the pen, and how the process differs from that of solid wood.
Todd Gunter
USA
Woodworking and woodturning were introduced to me at a young age and I was instantly hooked. Although I’ve worked with wood my whole life, I didn’t get serious about woodturning until 2014 at Showcase/Totally Turning Symposium. As a member of the NWA (Northeastern Woodworkers Association) and AWA (Adirondack Woodturners Association), wood turning and epoxy casting have become my focus.
While I don’t consider myself to be an artist, I do enjoy the endless creative opportunities presented through epoxy castings and then turning them. It is satisfying to look at a piece of wood (especially burls) and envision what to do with it. The end product doesn’t always conform to the image I had in mind, but something unique or a lesson will ensue. Even mistakes are artistic opportunities.
I served in the Marine Corps right out of High School for 27 years and retired in 2013 as a Master Sergeant. I currently work for the State University Construction Fund as a Data Warehouse Administrator in the IT Department. I’m also the Chairperson for the Totally Turning Symposium and a member of NWA, AWA, and AAW. In my “spare” time, casting and woodturning are my passion.
Demonstrations
- Safety guidelines
- Equipment involved
- Additional products (glitters, coloring, etc)
- Procedural practices
- Wood preparation for working with epoxy
- Review some tricks I’ve found to aid in deep epoxy pouring (and some I’ve seen but never tried myself)
- Do’s and Don’ts working with epoxy
- Working environment temperatures and humidity
- Questions are always welcome
- Safety guidelines
- Equipment involved
- Preparation procedures
- Equipment layout – VERY IMPORTANT!
- Working environment temperatures and humidity
- Questions are always welcome
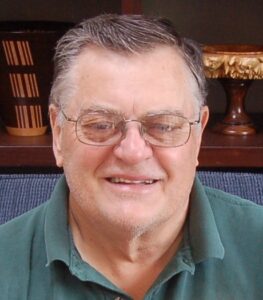
Ray Puffer
USA
Raymond Puffer (Ray) is a woodturner living in the Albany, NY area. He has been an avid woodworker for more than 60 years, and he has produced a broad variety of pieces ranging from custom designed grandfather clocks and furniture, to antique reproductions, guitars and banjos, and award winning artistic and functional turnings. His turnings have been featured in American Woodturner magazine. Ray is a member of the Northeast Woodworkers Association, the Adirondack Woodturners Association, the American Association of Woodturners, and the Segmented Woodturners.
Ray is a Registered Professional Engineer. He served a career as an Army officer, followed by a second career teaching engineering and leading industrial automation research programs at Rensselaer Polytechnic Institute in Troy, NY.
Ray is a frequent demonstrator at regional woodturning clubs and woodturning symposiums, and he teaches woodturning to individuals in his home shop. He exhibits and sells his work in regional art galleries and shows.
Demonstrations:
Mini hollow forms
Creating a thin-walled hollow form with an opening of only ¼” requires a steady hand and tools custom made for the task. In this demonstration I will discuss the selection of woods for these small turnings, and how I make the tools needed to hollow through a very small opening. I will demonstrate how I hold the turning, the hollowing techniques I use, along with measurement tools and finishing.
Patina, color and texture
In this demonstration I will present three of the embellishment techniques that I frequently use in my shop: gilding, mother of pearl inlay, and patination. While I mostly use these techniques with my woodturnings, they apply just as well to any form of woodworking. I will demonstrate how I apply these three embellishment techniques, and discuss the materials used, sources of supply, and how to get compliments on your woodworking projects.