Showcase Presenters for 2025
Tom McLaughlin | Johnny Tromboukis | Peter Cooper | Worth Gretter
Kyle Hall | Charlie James | Barbara Raymond-LaPrease | Bill Laymon Sr.
Lie-Nielsen | Scott Oliver | Ken Page | Logan Simms | Aaron Smith | Bill Sterling
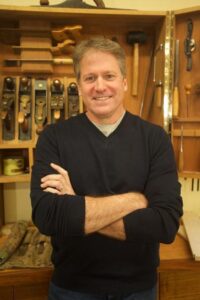
Tom McLaughlin
Tom McLaughlin apprenticed in the early 90s with Master Craftsman P.A. “Pug” Moore of Rocky Mount, NC. Over his 30+ year career he has designed and built a myriad of custom pieces for clients seeking to own pieces that are as much a work of art as they are functional.
As a 25-year member of the New Hampshire Furniture Masters, and former Chairman, his work has become recognizable for its dramatic use of figured wood, creating a sense of movement in each piece.
Tom can be seen on repeat episodes hosting Classic Woodworking with Fine Woodworking on PBS TV, and he’s a frequent contributor to Fine Woodworking Magazine.
In 2016, Tom shifted his focus from commission work to teaching on his Epic Woodworking platform. He and his wife Kris enjoy furthering the craft by providing resources and instruction for all levels through a free weekly livestream called Shop Night Live on YouTube, Online courses, and In-shop classes at his shop in Canterbury, NH.
They also offer a community Membership experience called “The Neighborwood” which brings together woodworkers from all over the world with the goal of expanding skills and inspiring creativity.
Be sure to check out Shop Night Live, Thursdays at 7:30 pm ET. Each week Tom goes live from his Shop and demonstrates tips and techniques or walks viewers through a small project. It’s free – catch the link here each week: epicwoodworking.com/SNL. Can’t watch it live? There are over 200 episodes archived at the Epic Woodworking YouTube channel, check them out anytime!
If you’ve yet to experience his teaching style, you’re in for a treat as he clearly delivers concepts for those at various levels of expertise to understand, with professional skill and a disarming humor. In addition, Tom is always glad to field questions throughout.
Demonstration:
Using Veneer to Complement Solid Wood Furniture
When making a piece of furniture, the choice doesn’t have to be either solid wood or veneered…why not both? In this presentation Tom will show several techniques for enhancing solid wood designs with veneer. He’ll use practical and photo examples to demonstrate how table legs, rails, drawer fronts and more can be dramatically raised to the next level with the selective and strategic use of veneer.
_______________________________________________________________
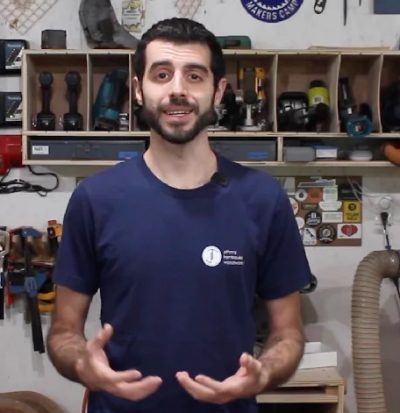
Johnny Tromboukis
Johnny Tromboukis is a fine woodworker who specializes in kumiko Japanese woodworking. His goal is to educate and inspire new and seasoned woodworkers. Intricate Japanese lattice work called kumiko is a big part of his work and a discipline within woodworking that he’s passionate about teaching and sharing with others. His YouTube channel is a way to do so and he also offers tools and kits on his website to help expand the skills of the awesome woodworkers within the DIY community. He has also been featured in Fine Woodworking Magazine and his pieces have been featured in galleries, podcasts and other media productions.
Demonstration: Kumiko
Presentation to cover tools, jigs, patterns and other things to know to be successful at Kumiko.
_______________________________________________________________
Peter Cooper
Peter is the owner of a Florida based company, whose dedicated team has been working to keep people safe since 2013. The company has specialist purveyors and distributors of PPE and CBRN training for the military and medical industries worldwide with a variety of clients from top military and medical organizations. They also provide the highest quality in PPE protection for a variety of industries and hobbyists including factory workers, chimney sweeps, and woodworkers.
Topic:
Safety for the Woodworker
Demonstration:
Peter will present the case for the correct respiratory protection for people exposed to harmful wood dusts. Peter will review the problems of short-, medium- and long-term effects of exposure and highlight the various products/solutions available.
_______________________________________________________________
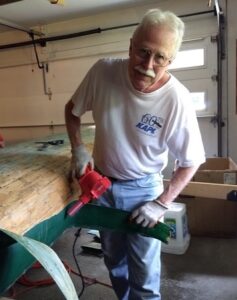
Worth Gretter
Worth grew up in the countryside of northwestern New Jersey, where his family built his father’s ultra-modern dream house for all of Worth’s childhood. Him and his brothers were the unpaid workforce! His ex-wife and he subsequently built a colonial-style house in Duanesburg in 1988, but they were the general contractors and did most of it with sub-contractors. And as always there are things to fix, update, or modify wherever you live.
Much of his woodworking over the years has been simple furniture, such as bookcases, platform beds, shelves, CD racks, things like that. And boats of course. Worth and his brothers built a Folbot kayak from a kit in high school. Later, he lived on a 40-foot fishing boat on the island of Crete for a year and a half, mostly working on the boat and doing very little traveling! Back in the US, he subsequently did repair and restoration on a couple of sailboats, as well as three modern fiberglass canoes (all “rescues”) before undertaking the wood and canvas canoe.
Topic: Canoe Restoration
Demonstration: Presentation will include a discussion of the main things that need fixing, such as:
- ruined rib ends and stems from rusted iron nails
- impact damage to ribs and planks
- just plain wood rot due to improper storage (such as upside down on the ground)
- blackened varnish on the interior
- often, fiberglass on the exterior that needs removal
- The new parts I made included:
- replacement rib ends for all 88 ribs
- new inner and outer gunwales
- seats
- and most challenging of all, new stems at both ends (needed to be steam bent)
- Finally of course:
- smoothing the hull exterior
- varnish and waxing
- covering with canvas (or in this case, Dacron)
- filling the fabric weave and painting
_______________________________________________________________
Kyle Hall
Kyle has been chainsaw carving since 2015 where he carves bears, eagles, moose, and owls. He is the owner of Hall’s Stick Furniture & Signs in Johnstown, NY and can be found on YouTube Channel – Kyle Hall Woodworker. Kyle also builds rustic furniture since 2010 and has entered many of his pieces in past Showcase events
Demonstration:
Kyle will be demonstrating his chainsaw process for making sculptures.
_______________________________________________________________
Charlie James
Charlie took up woodworking in high school shop class. He taught woodworking in adult education classes as extra credit while still in high school. He always did woodworking of some type while doing other jobs but after retiring he joined the Long Island Woodworkers (LIW) club. He took classes with Mario Rodriguez at (of all places!) FIT in NYC. It was a feeder class for students that were interested in working for museums repairing and restoring antique furniture. He has had quite a few of his tips published in FWW. He performs many demonstrations at the LIW club on many different types of woodworking such as working with veneer, and hide glue, cabinetmaking and making your own inlays as well as cutting in inlays or making jigs and tools from scrap wood and scrap steel. He was the winner of the Best of Show in Showcase 2023 for his tabletop desk with many hidden compartments and inlays. He was also the winner of the people’s choice award for Showcase 2016.
Demonstration:
Dovetails
_______________________________________________________________
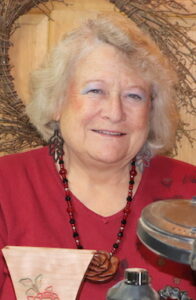
Barbara Raymond-LaPrease
Barbara Raymond-LaPrease is a member, secretary, newsletter editor and webmaster for the Woodworkers of Central New York (WWCNY). Barbara started scrolling around 1997 after Dale Whistler visited the Syracuse club to demo scrolling. Her first scroll saw needed to be clamped to a workbench to prevent it from bouncing and used only pinned blades. Her husband, Charlie, bought her a Delta 16” VS saw for Christmas that year and the rest is history!
Several years later, she added a 26” RBI to her saw collection so she’d have the throat depth for large puzzles. In 2008, her husband bought her an Excalibur after they tried them at a Canadian show. Barbara doesn’t necessarily specialize in any one type of scrolled art. One day it could be jewelry like earrings or necklaces whereas the next day she could be cutting detailed ornaments, pictures, boxes, or puzzles. Sometimes she combines her various talents, adding beaded accents to scrolled pieces. Barbara creates whatever she feels like with most items given as gifts, donated for raffles, or donated for club charitable sales.
Attending Showcase yearly since 2003, Barbara and her husband also routinely enter their projects for judging. Barbara has often helped at the Scrolling SIG booth during Showcase. She demonstrated faux marbling at Showcase in 2009. Her and her husband assist John Olenik to organize the Showcase display hall on Friday afternoon/evening. Barbara is a librarian by training but wandered into the IT arena by default. She worked for the local public utility in various jobs (including technology transfer coordinator and librarian) for 31 years before retiring in Sept 2012 after a life-threatening bout of breast cancer.
She and Charlie live on an 8-acre property outside Baldwinsville, NY where they host many of WWCNY’s events. They acquired a WoodMizer in 2022 so she has an endless supply of wood in addition to the collection they already had. The club’s workshop is in their large garage. If you attend the NYS Fair, you can find her in the club’s 300 sq foot demonstration in the Witter Agricultural Museum where she and fellow club members demonstrate non-electrified woodworking throughout the Fair.
Demonstrations:
1. Compound Cutting for 3D Puzzles
2. Introduction to Intarsia
_______________________________________________________________
Bill Laymon Sr.
Bill started woodcarving and woodworking in 1967 as a Boy Scout. In high school, he took every available shop class, plus a few independent study shop classes. After high school, for seven years, he worked as a machine operator, machinist, and cutter grinder while doing woodworking as a very serious hobby. At this juncture, he started my professional woodworking career as a contractor. After about 14 years as a contractor he went to college and got a teaching degree where he taught Building Trades at a BOCES for 20 years and retired in 2017. He is currently in his 20th year teaching spoon carving, canoe paddle carving, and bench building for the local 4-H Camp.
Topic:
Wood movement, shrinkage and their effects on joinery.
Demonstration:
The presentation will talk about wood movement, shrinkage and how these issues affect joinery. Knowledge of these issues can assist when picking lumber for a project.
_______________________________________________________________
Scott Oliver
Scott Oliver has been woodworking for over 25 years. His education has been varied including taking classes at RITs School for American Craft and, lately with Peter Galbert. Scott was a professional blacksmith for over a decade, during which time his interest in natural finishes grew. For the past three years Scott has focused on green woodworking and making stick chairs in his backyard workshop in Albany.
Topic:
Safe(er) Wood Finishes
Demonstrations:
Many finishes used in woodshops can contain chemicals that can be harmful to your health. Come learn about the following finishes which are time tested and have no VOCs.
• Milk Paint: This centuries old mixture containing milk proteins, lime, and clay is a versatile finish that’s flexible and can last for years.
• Linseed Oil: Learn how to make blown linseed oil with some basic equipment that takes flaxseed oil from the supermarket and turns it into a beautiful finish that dries in a few hours.
• Waxes: Beeswax and carnauba wax can be mixed with tung oil or linseed oil to create both hard and soft waxes which can protect furniture and bring out the beauty of wood’s grain.
This presentation will show basic techniques in mixing milk and applying milk paint and oil/wax mixtures and provide resources so woodworkers can start using them in their shops.
_______________________________________________________________
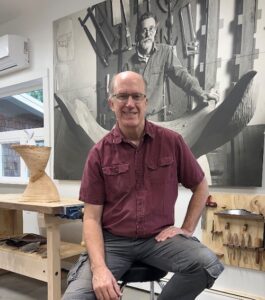
Ken Page
Ken Page is the director of the Wendell Castle Workshop (WCW), a nonprofit woodworking and metalworking school based in the former studio of the renowned Wendell Castle, widely recognized as the Father of the Art Furniture Movement. Castle’s groundbreaking work revolutionized the world of furniture design, and his legacy continues to inspire artists and makers today.
Before taking on the role of inaugural director at WCW, Page had a diverse career that bridged engineering and craftsmanship. While he was a part-time woodworker, he spent the majority of his professional life as an engineering program director in industries ranging from aerospace and automation to chemical manufacturing. This multifaceted background has equipped him with a unique skill set in leadership, project management, and team building—all of which have been instrumental in establishing and growing the Wendell Castle Workshop. Under his direction, WCW has become a dynamic hub for creativity, education, and artistic collaboration.
Topic:
A Second Life for the Wendell Castle Studio
Presentation:
Wendell Castle, widely considered the Father of the Art Furniture Movement, has left a lasting legacy that continues to influence studio furniture makers, sculptors, and artists across disciplines. Conference attendees will have the rare opportunity to learn about the transformation of Wendell’s longtime studio—from a space where he created his iconic, large-scale works to a vibrant hub for woodworking and metalworking education, now home to the Wendell Castle Workshop (WCW). Despite the transition, the essence or “DNA” of the original studio has been preserved, allowing it to remain a powerful source of inspiration for all who enter.
For many years, Wendell’s studio also served as his family home, and a section of this historic space is now dedicated to WCW, offering classes and artist residencies. The workshop is a living tribute to Wendell’s creative spirit, with walls adorned by photographs of his work, images of him in the studio, and displays of his original sketches. The studio also has an on-site gallery, which features not only Wendell’s work but also pieces by his widow, Nancy Jurs. By working in the same space where Wendell crafted his groundbreaking masterpieces and using the very tools and machinery he once employed, WCW students and resident artists are deeply immersed in the environment that nurtured his vision. This unique experience sparks creativity and encourages the next generation of makers to push the boundaries of their own craft.
_______________________________________________________________
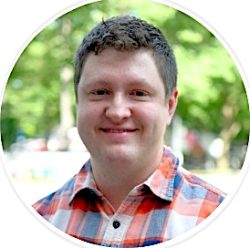
Logan Simms
Logan started woodworking with a gifted class for his 18th birthday and has never stopped since. He learned the traditional hand tool methods as taught by Welsch Master Artisan, Paul Sellers with supplemental skills learned at the Vermont School of Woodworking, and the Connecticut Valley School of Woodworking, and the Adirondack Folk School. He has taught classes throughout his home state of NY, most notably with the New Legacy School of Woodworking, Maplewood Center for Common Craft, and Saratoga Joinery. Logan has been an on and off NWA member since 2012 and meets with the Carver’s SIG, Turner’s SIG, and the Hand Tool SIG.
Topic 1: Mortise and Tenons
Topic 2: French Polishing
French polish is not a product. Rather, French polishing is a method of applying shellac to wood furniture, musical instruments, or decorative accents in many thin layers that results in a highly glossy, glass-smooth surface with a rich depth that beautifully highlights the grain of the wood. While it’s been around since the 1600s, French polish today has somewhat fallen out of favor, due to its labor-intensive process.
_______________________________________________________________
Aaron Smith
Aaron Smith is the owner of benchandchisel.com an online store specializing in refurbished antique handsaws. He offers hand saw sharpening services and speaks about saw sharpening at woodworking and hand tool clubs.
Demonstration:
Saw Sharpening
_______________________________________________________________
Bill Sterling
Bill Sterling is a retired art teacher with 30 years’ experience. He has been building guitars for 17 years and teaching guitar building for 11 years. He studied with Dave Nichols at Custom Pearl Inlay in Malone, NY. Bill is the President of the Hudson Valley chapter of the Northeast Woodworker’s Association. He teaches instrument building at Hudson River Maritime Museum boat school.
Demonstration:
Guitar Building
_______________________________________________________________